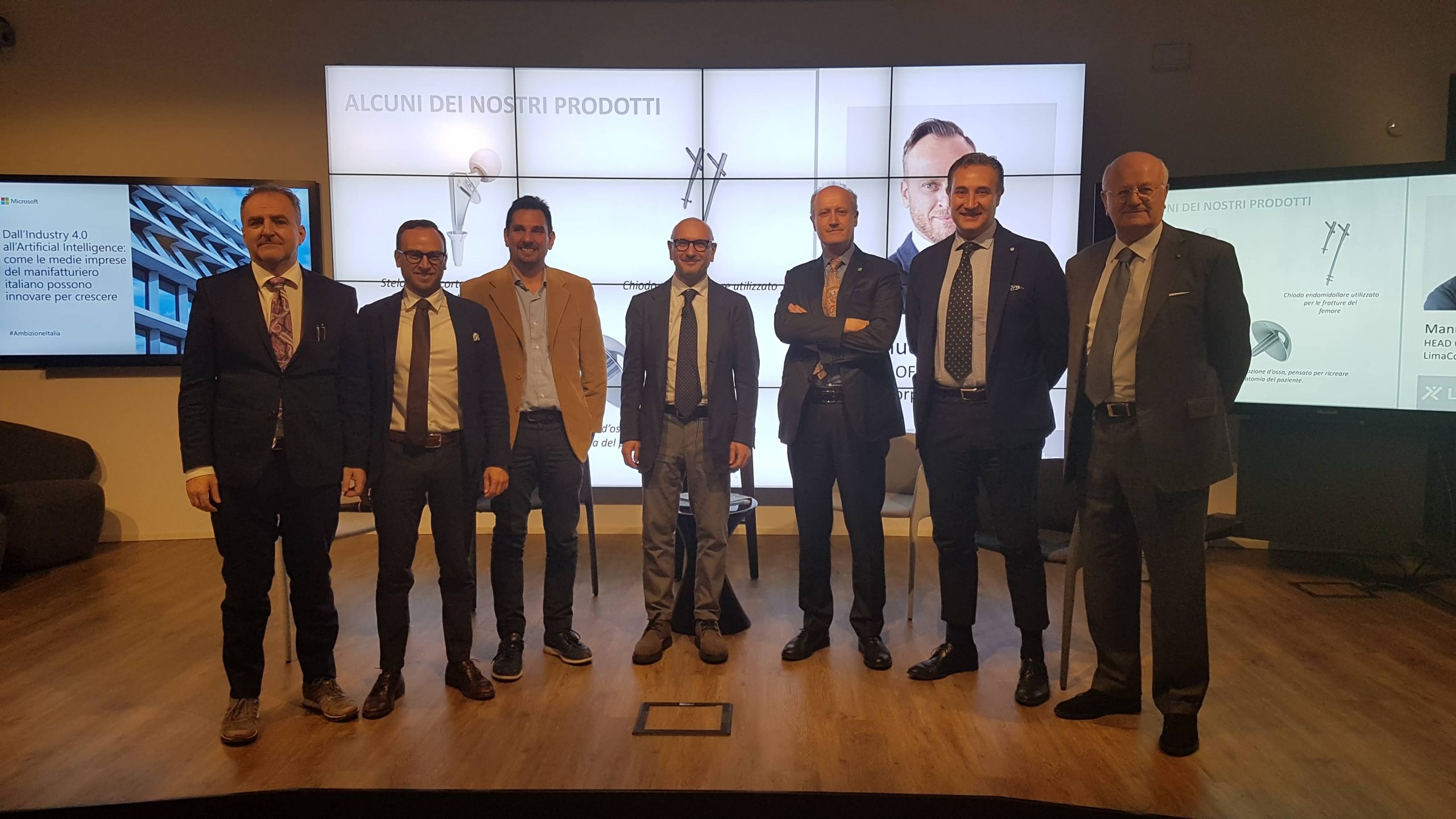
Miglioramento continuo in fabbrica: una strategia attuabile solo a fronte di un cambiamento di approccio

Le aziende manifatturiere da sempre sono strutture molto complesse che uniscono un’anima più rivolta al “fare” e una agli aspetti strategici.
Più queste due metà lavorano in modo sincrono e si muovono verso la stessa direzione, più la realtà sarà capace di raggiungere gli obiettivi prefissati. Non si tratta però solo di una concatenazione di azioni correlate una con l’altra da portare a termine nel minor tempo possibile, quanto piuttosto di una serie di scelte da studiare a monte basate su ragionamenti strategici di posizionamento dell’azienda di oggi e di domani.
L’ottimizzazione dei processi ieri e oggi: come il miglioramento continuo entra in gioco
Il concetto di continuous improvement ha molteplici sfaccettature declinabili a seconda del settore o addirittura della specifica realtà aziendale.
In generale, se ci addentriamo nel mondo manifatturiero, possiamo notare come i parametri di produttività (dei plant e degli operatori) e il costo delle materie prime sono i due aspetti chiave.
Oggi, si innesta un terzo KPI che è più orientato a tematiche legate al cliente, alla sua soddisfazione nello scegliere un prodotto che sia di qualità, e proveniente da un’azienda che crede e persevera delle scelte sostenibili, agili e solide/affidabili.
Se in passato, il paradigma era produrre di più e a minor costo, oggi e in futuro l’orientamento sarà verso il produrre meglio.
Questo nuovo concetto cambia radicalmente la prospettiva delle aziende manifatturiere moderne che quindi hanno come obiettivo principale l’efficientamento; non solo però dei processi strettamente legati all’ambito produttivo, ma di tutti gli ambiti che compongono l’ecosistema rivoluzionando a tutto tondo l’approccio di “persone e cose” che lo compongono per arrivare ad un ambiente industriale più sostenibile.
Sostenibilità nel continuous improvement: non solo “green”, ma anche “lean”
Spesso si pensa al termine sostenibilità come a qualcosa di legato solo a tematiche “eco-green”; in questo caso, invece, la prospettiva è molto più ampia e va a toccare anche temi legati all’approccio aziendale verso un nuovo metodo di lavoro.
In quest’ottica, la sostenibilità si avvicina molto al termine “lean”, che ha come ultimo scopo l’efficienza e l’ottimizzazione.
L’idea di lean ha iniziato a circolare negli anni 40 del Novecento, per consolidarsi poi negli anni 90 all’interno di un metodo ben preciso composto da cinque pilastri basati sulla teoria di James Womack e Daniel Jones:
- Individuare il valore;
- Mappare il flusso di valore;
- Creare il flusso;
- Stabilire un sistema pull;
- Perseguire la perfezione.
Questo flusso all’apparenza astratto, se calato nella concretezza di un contesto manifatturiero e utilizzato come guida per disegnare la miglior strategia adatta ad un contesto specifico, è molto utile e può davvero rivoluzionare l’ecosistema produttivo rendendolo più efficiente giorno dopo giorno.
Il bello, infatti, di questo metodo è il fatto che non esiste una “fine”, un punto di arrivo oltre il quale non è possibile evolvere, quanto piuttosto è in continuo miglioramento e si “aggiusta” adattandosi ai cambiamenti di mercato, di trend o di esigenze interne dell’azienda.
Trovare le best practise che fanno al caso tuo
Trovare metodi sempre migliori di lavoro è un aspetto chiave nella cultura lean. Evidenziare quindi pattern, situazioni, KPI e capire come e quando ripeterli agevola l’efficientamento della produzione e aumenta la disponibilità di linee e operatori.
Per individuare le best practise e i “settaggi” di macchinari, allocazione di risorse interne e materie prime ideali ci sono due metodologie:
- Una tradizionale dove le raccolte di informazioni avvengono “manualmente” e unendo tutti i dati utili su file statici
- Una più evoluta dove gli strumenti digitali e tecnologici possono supportare l’individuazione di pattern positivi per poi fare delle considerazioni strategiche ad ampio raggio
La seconda strada è sicuramente l’opzione che impatta in modo considerevole in una prima fase l’organizzazione e la riorganizzazione interna (nuovi strumenti, nuovi metodi di lavoro e formazione del personale), ma è anche quella che una volta calata bene all’interno della realtà produttiva porta degli enormi risultati che si migliorano sempre di più con il tempo.
Quali soluzioni tecnologiche scegliere per arrivare ad un continuo miglioramento dei processi di fabbrica
Per un’azienda manifatturiera che si pone come obiettivo l’efficientare il processo nella sua interezza ed arrivare a migliorare continuamente le scelte fatte sulla base delle modifiche richieste dal mercato, più è presente e stabile la tecnologia meglio e più facile diventa tutto il percorso.
La digitalizzazione delle varie fasi produttive è infatti un abilitatore di raccolta di informazioni a valore capace di suggerire cosa è meglio fare per un ambito specifico, in modo tale che la propagazione dell’efficientamento migliori anche gli altri aspetti implicati nel processo.
Le soluzioni tecnologiche a disposizione sono le più svariate e non esiste una scelta in assoluto migliore di un’altra, per orientarsi meglio in quale opzione ricadere è bene tener presente alcuni aspetti come:
- Quanto è facilmente integrabile all’interno dell’ecosistema produttivo;
- Quanto è complicata la soluzione e quanto il personale implicato nel progetto è pronto a utilizzarla:
- Quanto tempo necessita per essere implementata e con quali costi;
- Quando avverrà il ritorno dell’investimento e se si verificherà.
Una volta fatta una valutazione dei pro e dei contro delle proposte a disposizione ed esaurite le valutazioni sopra citate, la scelta del sistema digitale più adatto alla mia realtà diventa più semplice.
Il percorso di digitalizzazione, un processo continuo (di miglioramento)
La digitalizzazione dei processi di fabbrica è un percorso in continua evoluzione che punta, anch’esso, a migliorarsi continuamente ridisegnando e sistemando strategie e metodi in base a come evolve l’azienda al suo interno e rispetto al mercato esterno.
Non è importante da che punto si parta, quanto piuttosto dare una scala di priorità sulla base dell’impatto che quell’ambito specifico ha a cascato sugli altri.
Una volta delineato il percorso adatto alle esigenze aziendali, è importante dotarsi da una parte delle soluzioni tecnologiche giuste agli obiettivi, dall’altra del supporto consulenziale e di competenze in linea con la struttura organizzativa e di business.
La scelta di un system integrator non si basa infatti solamente sulle soluzioni a portafoglio, ma anche su che team di progetto è messo a disposizione lungo tutto il percorso, quali conoscenze e certificazioni hanno verticalmente in quell’ambito, che supporto formativo viene dato alle figure interne all’azienda. Tanto più il fornitore ha capacità di rispondere a questi punti con completezza, maggiore sarà la rilevanza strategica di sceglierlo rispetto ad altre proposte.
BEANTECH: le caratteristiche che fanno la differenza
beanTech è cresciuta negli anni con l’obiettivo di diventare unico punto di riferimento per le aziende manifatturiere che hanno l’obiettivo di digitalizzare i processi di fabbrica. Per fare questo ha creato un hub, ad oggi di 250 persone, composto da figure di alta competenza che abbiamo dimestichezza, certificazioni e competenze nei contesti di produzione.
L’attributo differenziante è infatti che, al di là del punto di partenza, una realtà ha la possibilità di digitalizzare – passo dopo passo – ogni singolo aspetto organizzativo senza mai cambiare interlocutore e attingendo ad un supporto consolidato e fatto di figure altamente professionali dove ogni progetto e soluzione è studiata e calata nella specificità aziendale.
In quest’ottica l’azienda-cliente e beanTech diventano due entità che lavorano all’unisono per rendere tutto il processo più efficiente e ottimizzato, cercando le strategie e soluzioni più adatte e che possano portare ad un continuo miglioramento e trasformando il processo da una strada a linea retta ad un circolo virtuoso sempre migliore.
Migliorare la qualità: un punto di partenza per un obiettivo più ampio
Il percorso evolutivo dei processi industriali verso un nuovo approccio di miglioramento continuo implica un inizio.
La soluzione DeepInsight powered by beanTech unisce dati e immagini di una linea per creare correlazioni, tramite l’AI, tra difetti/errori e pattern di produzione. Il sistema è in grado di suggerire delle azioni migliorative, sulla base dei dati storici, con lo scopo di migliorare sempre di più gli aspetti qualitativi.
Ottimizzare i parametri di qualità ha a cascata una serie di implicazioni positive su tutto il processo e sulla soddisfazione del cliente finale che non hanno mai un punto di arrivo e anzi si possono sempre più efficientare.
Questo fatto è successo ad aziende che hanno scelto di inserire il sistema DeepInsight nelle loro linee ottenendo risultati oltre ogni aspettativa, con KPI migliorativi rilevanti (qui il case per approfondire). E al di là di parametri che la realtà industriale si aspettava di raggiungere nel percorso evolutivo, sono arrivate delle sorprese inattese che hanno accelerato ulteriormente il processo di digitalizzazione e di miglioramento che avevano intrapreso.
Oggi infatti, l’azienda è in grado di manutenere i propri macchinari e impianti in modo predittivo e preventivo solo grazie all’analisi dei dati e alle correlazioni che il sistema è in grado di fare tra essi, suggerendo addirittura al produttore di origine come meglio andare a produrre i macchinari stessi che commercializza.