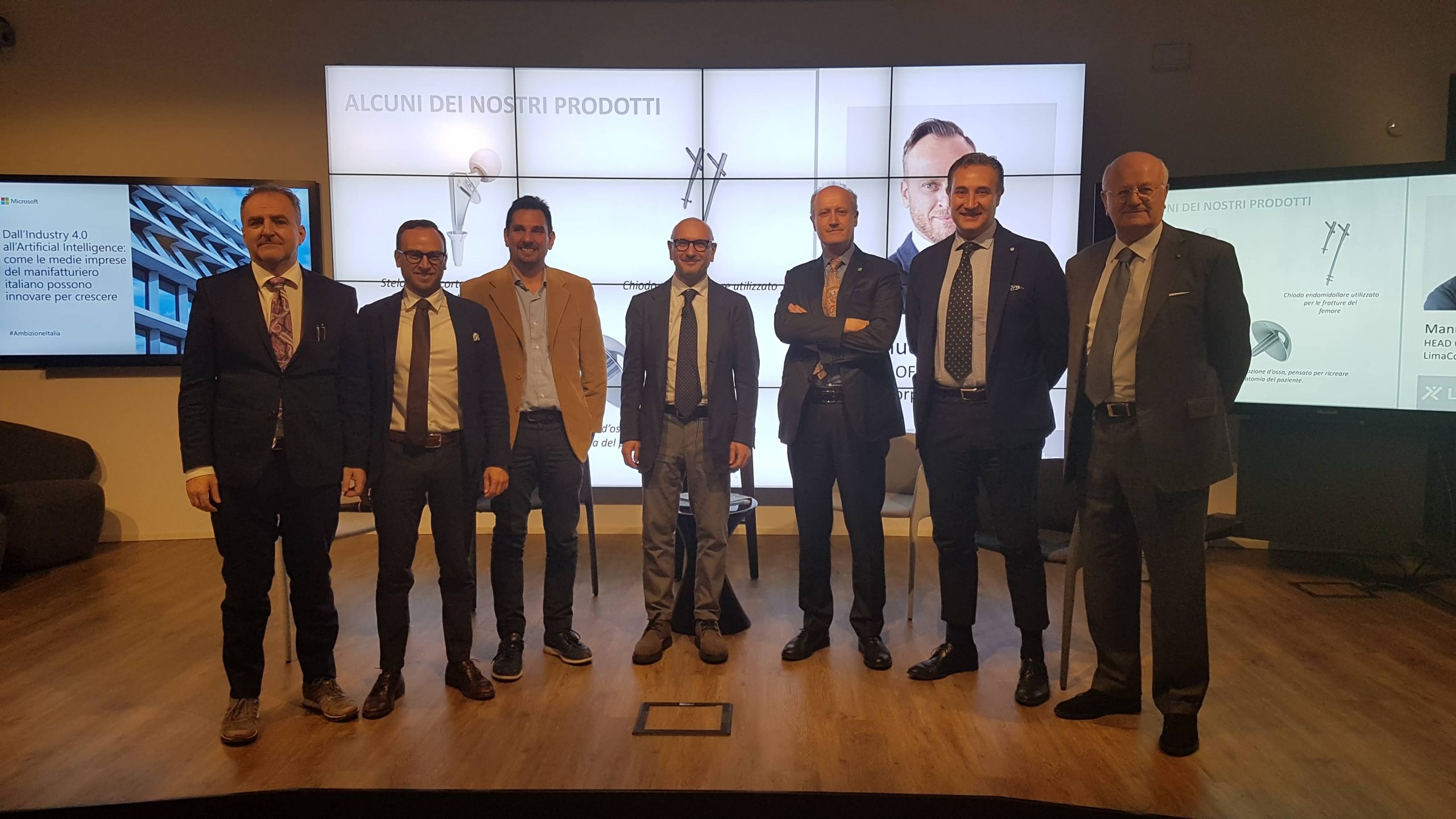
5 (buoni) motivi per cui non potrai più fare a meno dell’intelligenza artificiale nel tuo impianto industriale

L’intelligenza artificiale pervade ormai ogni cosa e noi la usiamo, più o meno consapevolmente, nella nostra quotidianità. Se nella sfera privata l’AI è stata ben intesa da tutti noi come uno strumento valido e di supporto per le nostre azioni (Alexa, Google Home, ecc.) e che ci mette a disposizione le informazioni che preferiamo (ad esempio gli algoritmi social), nella sfera lavorativa non è ancora stato inteso al 100 % il valore del “grande cervello”. Non sappiamo ancora bene come utilizzare l’IA, cosa farcene, che risposte ci può fornire per “fare meglio” il nostro lavoro e che informazioni dargli in pasto per farla apprendere.
L’intelligenza artificiale nel settore industriale
In ambito industriale, ad esempio, sta accadendo una rivoluzione, ma ne siamo totalmente consapevoli e siamo pronti per cavalcare questa nuova era utilizzando ciò che la tecnologia ci mette a disposizione?
Con l’avvento dell’IoT e quindi dell’opportunità di connettere ogni dispositivo alla rete, le soluzioni industriali che utilizzano componenti di intelligenza artificiale al loro interno hanno avuto un’impennata senza precedenti. Oggigiorno non esiste un sistema che non abbia al suo interno, anche se in minima parte, un algoritmo che studi e apprenda dai dati di produzione.
Ma come fare per capire appieno le potenzialità di questo strumento e inserirlo al meglio all’interno del proprio contesto di business? Che cosa devo chiedere all’intelligenza artificiale? Quali informazioni devo metterle a disposizione e che risposte potrà darmi per migliorare il mio processo produttivo?
Se queste sono le principali domande che ti poni ogni volta che approcci delle soluzioni digitali volte ad aumentare le performance della tua fabbrica, potenziare la qualità dei tuoi prodotti e monitorare i consumi energetici, allora questo articolo è fatto per te. E ti spieghiamo il perché in 5 (buoni) motivi.
1. Studiare i dati per conoscere nel dettaglio tutto il processo produttivo
All’apice di tutte le motivazioni che rendono l’intelligenza artificiale un vero alleato per le produzioni industriali c’è la possibilità di analizzare i dati. Raccogliere informazioni da sistemi eterogenei, normalizzarli, validarli, pulirli e studiarli porta infatti ad un vantaggio competitivo non indifferente. L’intelligenza artificiale offre un supporto senza precedenti per conoscere a fondo i processi operativi di un’azienda manifatturiera, aiutando i vari attori aziendali a trovare correlazioni tra causa-effetto, set-up ottimali, stagionalità e ottimizzazioni produttive in termini di qualità, consumi energetici, manutenzioni a impianti e/o macchinari. Gli algoritmi hanno una grande “fame” di dati (ricavabili dal proprio storico) con cui apprendere sempre di più per migliorare e ottimizzare i processi in questo caso industriali (ma non solo).
2. Fare modelli predittivi per anticipare eventi
Partendo sempre dal concetto che l’AI apprende analizzando i dati che gli vengono dati in pasto, l’algoritmo diventa sempre più capace nel sottoporre miglioramenti e raccomandazioni sul come meglio gestire il proprio impianto. Ad esempio, in ambito manutenzione, è in grado di rilevare in anticipo segnali precoci di guasti imminenti aiutando gli operatori ad agire in precedenza evitando fermi macchina.
Oppure in ambito service, il sistema viene in supporto nel proporre al reparto come meglio offrire ai propri clienti un’assistenza proattiva e preventiva, offerte di ricambistica e/o di ore di assistenza sempre più personalizzate a seconda dell’utilizzo dei macchinari.
3. Ridurre i costi per fare un nuovo prodotto
Come faccio a mettere in produzione un nuovo prodotto secondo le linee guida richieste dai miei clienti e le capacità del mio impianto? Grazie all’IA è possibile mettere in piedi dei modelli previsionali “cosa succede se…”, dove le aree di Ricerca & Sviluppo sono capaci di fare dei test e avere degli output in anteprima sulla migliore ottimizzazione e fattibilità di un nuovo prodotto.
Anche in questo caso entra in gioco lo storico dei nostri dati che, arricchito delle “nuove” informazioni inserite all’interno del sistema, ci può dare una previsione molto vicina all’effettivo realizzo.
Questa opportunità si applica molto bene a settori come il farmaceutico in cui è presente una composizione chimica particolare. In questo caso, invece di demandare la sperimentazione ad un laboratorio dedicato, è sufficiente inserire i dati specifici della ricetta in modo tale da capire che risultato si ottiene, se va migliorato/ modificato oppure totalmente stravolto per ottenere ciò che si sta cercando.
4. Monitoraggio dei consumi energetici e delle risorse
Mai tema è più centrale negli ultimi mesi come l’energia, le materie prime e il miglior uso che ne possiamo fare in ottica di risparmio e sostenibilità ambientale. L’IA viene in aiuto del settore industriale fornendo output che supportino nel diminuire i tempi morti e gli sprechi di consumo energetico, capire in che momento è più vantaggioso acquistare materie prime ed energia.
5. Inferenze vicino al campo
Se prima per misurare parametri come la temperatura era necessario che l’operatore manualmente facesse questa operazione, oggi è sufficiente accedere ad un dispositivo a bordo macchina che dia la lettura istantanea dei gradi con le relative proiezioni future. La capacità degli algoritmi di rielaborare i dati raccolti dal campo agevola la quotidianità di tutti gli operatori snellendo le azioni ripetitive e lasciando più spazio ad azioni di maggior valore oltre che a conoscere fino al più piccolo dettaglio tutto ciò che riguarda il sito produttivo.
RealSiGHT: la piattaforma per governare l’intero impianto con l’AI
RealSiGHT è la soluzione che interconnette ogni singolo dispositivo potenziando le performance dell’impianto industriale grazie all’AI. La piattaforma elabora e gestisce in tempo reale i dati provenienti da sensori delle macchine, sistemi di controllo e gestionali con l’obiettivo di governare in modo intelligente l’intero processo di produzione.
Con un unico strumento aspetti come le performance globali d’impianto, qualità, manutenzione ed energia sono monitorati nell’ottica di essere ottimizzati e migliorati.
Il sistema aperto e flessibile facilita l’installazione all’interno dell’ecosistema informatico già esistente delle realtà industriali agevolandone l’integrazione con MES, ERP, PLC, sistemi di controllo e processo.
Aziende come Volteco, a seguito dell’adozione di RealSiGHT, hanno riscontrato un aumento della produzione del 30 % e una diminuzione degli scarti del 37 % in pochi mesi.
Questi KPI dimostrano come, se un sistema avanzato di intelligenza d’impianto è studiato seguendo le reali necessità di settore specifico, sia un vero facilitatore per il business.