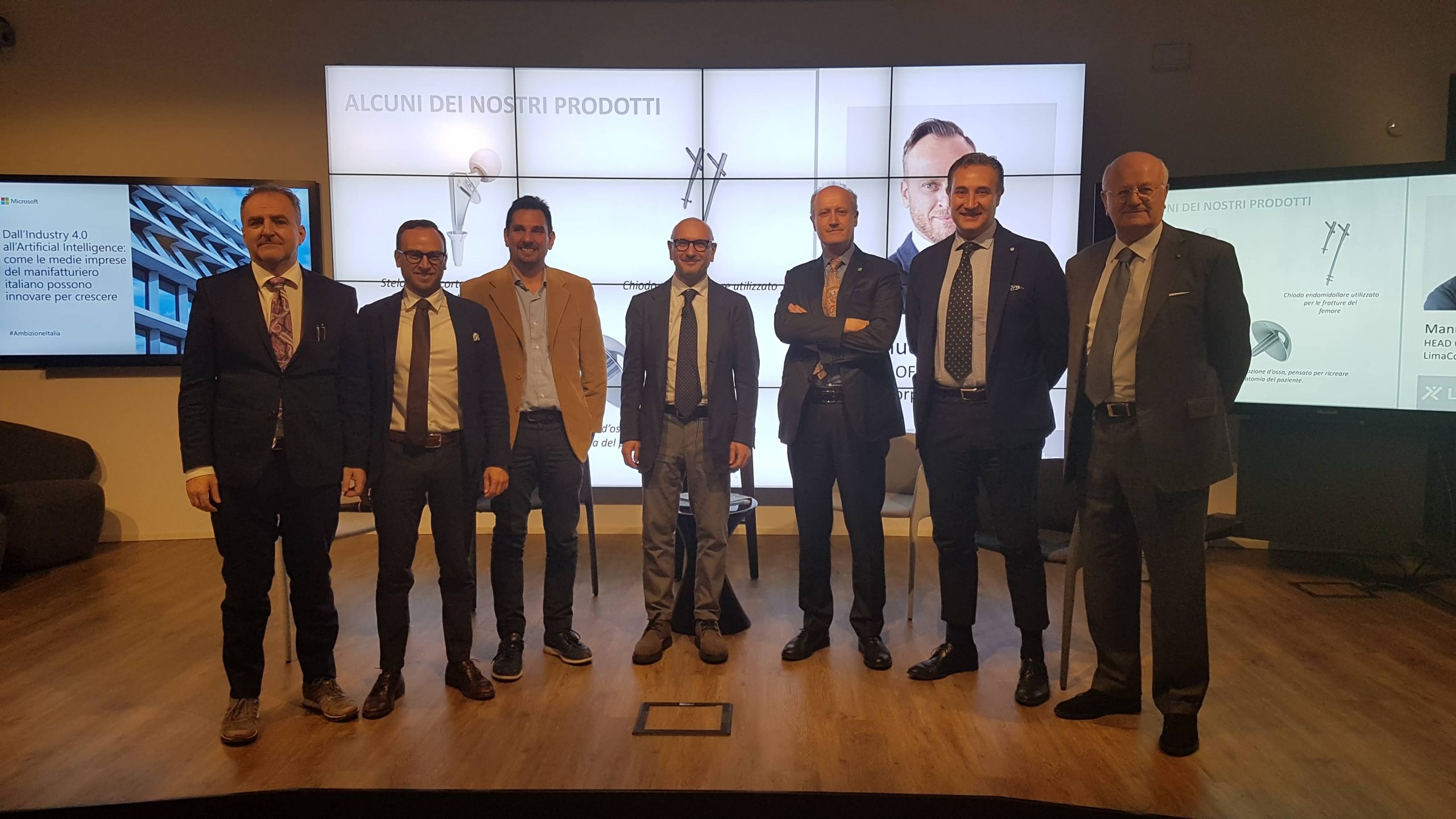
Le sfide dell’Operation Manager nell’era dell’IoT for Industrial Production
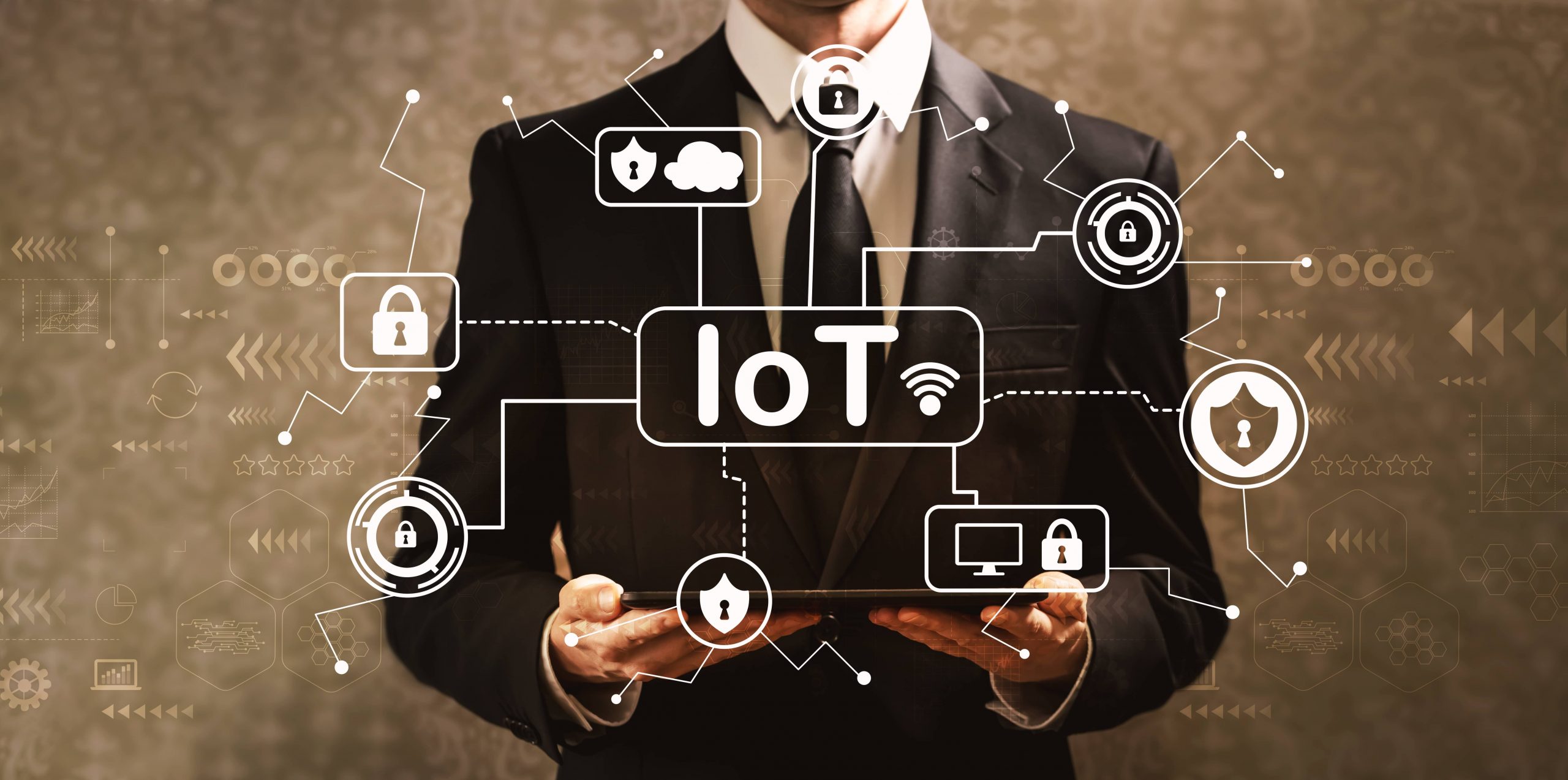
Se c’è una cosa che costituisce un’ossessione per gli Operation Manager è la continua ricerca dell’efficienza. L’ottimizzazione dei processi per aumentare la produttività e ridurre i costi è l’impegno principale che può trovare nuova linfa con l’Industrial IoT (IIoT).
Il termine IIoT descrive infatti, l’applicazione dell’IoT nel contesto dell’industria di quarta generazione e il suo scopo è appunto quello di ottimizzare il processo produttivo mettendo in comunicazione tra loro le macchine ed elaborando i dati che consentano un’analisi predittiva e quindi un notevole risparmio: consente di migliorare connettività, efficienza, scalabilità, risparmio di tempo e di costi per le organizzazioni industriali.
Le aziende stanno già beneficiando dell’IIoT attraverso risparmi sui costi grazie alla manutenzione predittiva, al miglioramento della sicurezza e ad altre efficienze operative. Le reti IIoT di dispositivi intelligenti consentono infatti alle organizzazioni industriali di rompere i silos e di collegare persone, dati e processi dallo stabilimento agli uffici direzionali.
Un mix di tecnologie
Alcuni produttori stanno facendo passi avanti su questa nuova strada utilizzando una combinazione di tecnologie per sfruttare big data e analytics e migliorare l’efficienza degli impianti, aumentare la produttività, ridurre i tempi di fermo produzione e il time-to-market e migliorare la qualità dei processi e dei prodotti.
Nel mondo industriale si sono già diffusi alcuni casi d’uso che dimostrano l’utilità dell’utilizzo dell’IIoT anche per gli Operation Manager.
Nel manifatturiero per esempio vengono raccolti i dati che si verificano in fabbrica e che possono rivelare carenze significative. Questi dati devono però essere raccolti in tempo reale e verificati, azioni rese più facili dall’utilizzo dell’IIoT che permette anche di analizzarli, trovare relazioni e supportare le previsioni di future non conformità. I processi operativi di un impianto con l’ottimizzazione dei suoi carichi rappresentano un’area critica di un’azienda manifatturiera.
In questo modo è possibile gestire il business e creare un sistema di comando e controllo che integra piani strategici di business e operazioni tattiche quotidiane. A seconda del ciclo di vita del prodotto, questi processi permettono di definire le previsioni di carico nel tempo, il che aiuta a determinare quali prodotti un’azienda produrrà e in quale impianto.
I progressi operativi
L’interesse delle aziende verso l’utilizzo di macchine dotate di sensori si spiega con la possibilità di attivare la manutenzione predittiva e il loro monitoraggio.
Le macchine utensili, infatti, sono progettate per funzionare entro determinati intervalli di temperatura e vibrazioni. I sensori sono in grado di monitorare attivamente e inviare un avviso quando la macchina si discosta da questi parametri prescritti e aiutare a prevenire malfunzionamenti.
Dal punto di vista della supply chain l’accesso alle informazioni in tempo reale sulla catena di approvvigionamento aiuta a identificare i problemi prima che si verifichino, riduce le scorte e potenzialmente il fabbisogno di capitale. Collegando gli impianti ai fornitori, tutte le parti coinvolte nella catena di fornitura possono tracciare le interdipendenze, il flusso dei materiali e i tempi del ciclo di produzione.
I sistemi abilitati per l’IIoT possono essere configurati per la localizzazione, il monitoraggio a distanza dell’inventario e il reporting di parti e prodotti mentre si muovono lungo la catena di fornitura. Possono anche raccogliere e inserire informazioni sulla consegna in ERP, PLM e altri sistemi.
Dati e analytics
La base di tutto per l’Operation Manager è la disponibilità di dati, la capacità di interpretarli tramite la Business Analytics, estraendo il valore per l’azienda. Quando con il piano Calenda è stato varato l’iperammortamento che incentiva l’acquisto di nuove tecnologie molti imprenditori hanno colto solo il vantaggio fiscale del provvedimento.
Ma dopo avere acquistato macchine 4.0 che permettevano lo scambio di dati tutti si sono accorti che la grande mole di informazioni poteva essere sfruttata utilizzando strumenti di analisi (modelli statistici, storicizzazione dei dati e altro) per il supporto alle decisioni, verifiche sulla produzione, risparmio di costi e in generale per ottenere quel valore aggiunto prima impossibile da ottenere.